How Diamond Dicing Blades Redefine Standards in Semiconductor Industry
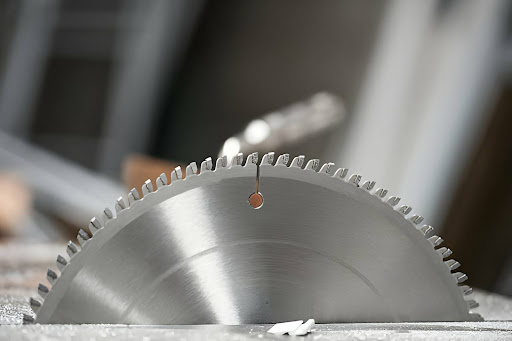
The semiconductor industry stands as a cornerstone of modern technology, powering the devices and systems that define our daily lives. From smartphones to medical devices, semiconductors are omnipresent.
Within this industry, precision is paramount, and every step in the manufacturing process must meet exacting standards to ensure optimal performance and reliability.
One critical aspect of semiconductor production is dicing – the process of cutting semiconductor materials into individual chips or dies. Traditional dicing methods often involve the use of blades made from materials like resin or metal.
However, recent advancements have led to the widespread adoption of diamond dicing blades, revolutionizing the semiconductor manufacturing process.
Evolution of Dicing Blades
Historically, semiconductor manufacturers relied on blades made from materials such as resin or metal alloys for dicing. While these blades served their purpose adequately, they were not without limitations. Resin blades, for instance, were prone to wear and deformation, leading to inconsistent cutting performance and reduced product quality.
Metal blades, on the other hand, exhibited better durability but lacked the precision required for cutting ultra-thin wafers and delicate semiconductor materials. The advent of diamond dicing blades marked a significant milestone in semiconductor manufacturing.
By harnessing the exceptional properties of diamond – the hardest known material – these blades offered unparalleled cutting precision, extended lifespan, and enhanced reliability. As a result, high-quality diamond dicing blades quickly gained traction within the industry, redefining the standards for dicing processes.
Unmatched Precision and Consistency
One of the most notable advantages of diamond dicing blades is their unparalleled precision and consistency. The inherent hardness of diamond ensures that the blades maintain their sharpness over prolonged use, enabling them to cut through semiconductor materials with remarkable accuracy.
This level of precision is crucial, especially when dealing with advanced semiconductor technologies that feature ultra-thin wafers and microscopic circuitry.
Moreover, diamond dicing blades exhibit minimal kerf width – the width of material removed during cutting – resulting in narrower streets between individual chips. This not only maximizes the number of chips obtained from a single wafer but also reduces material waste, contributing to cost efficiency in semiconductor manufacturing.
Enhanced Durability and Longevity
Durability is another key attribute that sets diamond dicing blades apart from their conventional counterparts. Unlike resin or metal blades that degrade over time, diamond blades maintain their cutting performance and structural integrity even after prolonged use.
This extended lifespan translates to fewer blade replacements, minimizing downtime and maintenance costs for semiconductor manufacturers.
Furthermore, the exceptional hardness of diamond ensures that the blades are less susceptible to wear and deformation, even when subjected to high-speed cutting operations. This robustness is particularly advantageous in high-volume production environments where consistent performance and reliability are paramount.
Versatility Across Materials
Diamond dicing blades offer versatility across a wide range of semiconductor materials, making them suitable for diverse manufacturing applications. Whether cutting silicon, gallium arsenide, silicon carbide, or other semiconductor substrates, diamond blades deliver consistent results with minimal chipping and surface damage.
This versatility enables semiconductor manufacturers to streamline their production processes and adapt to evolving material requirements without compromising on cutting quality.
Additionally, diamond dicing blades exhibit excellent thermal conductivity, dissipating heat generated during cutting more effectively than conventional blades.
This thermal management capability is crucial for preventing heat-related damage to delicate semiconductor materials, ensuring the integrity of the final product.
Advancements in Blade Design and Technology
The continuous evolution of diamond dicing blade design and technology has further enhanced their performance and efficiency in semiconductor manufacturing.
Advanced manufacturing techniques, such as laser cutting and precision grinding, enable the production of diamond blades with custom geometries and edge profiles tailored to specific dicing applications.
Furthermore, innovations in bonding methods have improved the adhesion of diamond particles to the blade substrate, enhancing overall blade strength and stability. This ensures uniform distribution of cutting forces and minimizes the risk of blade deflection or vibration during operation, resulting in smoother and more precise cuts.
Conclusion
In conclusion, diamond dicing blades have redefined the standards for precision cutting in the semiconductor industry. Their unmatched precision, durability, and versatility have made them indispensable tools in semiconductor manufacturing processes, enabling manufacturers to meet the demands of increasingly complex and advanced technologies.
As the semiconductor industry continues to push the boundaries of innovation, the role of diamond dicing blades will only become more pronounced.
With ongoing advancements in blade design and technology, these blades will continue to drive efficiency, quality, and reliability across the semiconductor manufacturing landscape, shaping the future of electronic devices and systems for generations to come.
You’ve done a remarkable job of covering this topic in depth. Thanks for the great read!